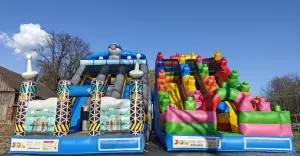
Wiadomości
- 3 lipca 2020
- wyświetleń: 8286
Valeo zmodernizowało swój zakład, aby uciec przed kryzysem
Kryzys spowodowany epidemią koronawirusa mocno uderzył w szeroko pojętą branżę motoryzacyjną. Formą ucieczki przed skutkami stagnacji może być modernizacja zakładów produkcyjnych. Jak informuje portal Wirtualny Nowy Przemysł, jedną z firm, która wykorzystała rozwiązania automatyzacyjne do budowy przewagi konkurencyjnej jest dostawca podzespołów - Valeo, który unowocześnił swój czechowicki zakład.
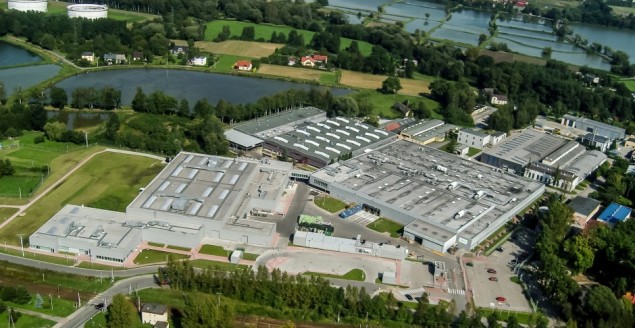
W wyniku kryzysu popytowego spowodowanego epidemią koronawirusa firmy otrzymują mniej zamówień, a w efekcie wyraźnie zmniejszyła się sprzedaż. Rosną też zapasy niesprzedanych towarów w magazynach. Jednak w Polsce większość firm nie tylko nie poddaje się pesymistycznym nastrojom w branży, ale przeciwnie - inwestując w automatykę szuka remedium na problemy związane z wahaniami koniunktury, dostępem do kadr, koniecznością obniżania kosztów i poprawy jakości wytwarzanych produktów. Przykładem może być firma Valeo, która prowadzi w Polsce produkcję w czterech zakładach: dwóch w Skawinie oraz po jednym w Czechowicach-Dziedzicach i Chrzanowie. Oddana niedawno do użytku półautomatyczna linia produkcyjna w Czechowicach-Dziedzicach pozwoliła firmie zwiększyć możliwości produkcji przepustnic samochodowych. Proces produkcji tych podzespołów zautomatyzowała firma teamtechnik.
- Dzięki wdrożeniu możliwe jest dostarczanie zupełnie nowego rodzaju podzespołu dla naszego klienta. W porównaniu do wcześniejszych linii produkcyjnych cykl wytwarzania jest znacznie krótszy, bardziej odporny na awarię i elastyczny. Zastosowane rozwiązania pozwoliły nam zwiększyć produkcję i obniżyć koszty. W ślad za tym wdrożeniem uruchomiliśmy kolejne linie produkcyjne unowocześnionych modeli przepustnic, ponosząc niewielkie nakłady inwestycyjne - powiedział portalowi Wirtualny Nowy Przemysł Jarosław Baranowski, Starszy Automatyk w Dziale Innowacji Technicznych Valeo.
Każdy z etapów produkcji w zakładzie w Czechowicach-Dziedzicach podlega ścisłej kontroli. Podczas montażu silnika, który jest przykręcany w urządzeniu, weryfikowany jest kąt i moment obrotowy wkrętarek. Natomiast podczas montażu koła zębatego kontrolowana jest siła i przemieszczenie montowanego elementu. Dane te przekazywane są w sposób cyfrowy z systemu urządzenia wykonującego tę czynność do systemu informatycznego MES (Manufacturing Execution System) służącego do śledzenia i dokumentowania przebiegu produkcji. System ten ułatwia optymalizację procesów produkcyjnych. Pozwala on m.in. na powiadamianie kierownictwa o możliwej awarii zanim się ona wydarzy, czyli predictive maintenance.
- Na podstawie przesyłanych do systemu MES informacji śledzących (traceability) oraz kodów błędów, wiemy o tym, jakie problemy wystąpiły podczas montażu. Zyskujemy dzięki temu cenną wiedzę pomocną nam w wykrywaniu potencjalnych awarii zanim one nastąpią. W ten sposób realizujemy koncepcję predictive maintenance, będącą jednym z elementów Industry 4.0. Na podstawie wspomnianych informacji udało nam się wykryć zależność między żywotnością elementu służącego do wkręcania, a jakością realizowanego procesu. W efekcie możliwe było ustalenie, jak często należy wykonywać przeglądy techniczne maszyn, by jakość realizowanych przez nie czynności nie ulegała pogorszeniu, i jak uniknąć niepotrzebnych przestojów - stwierdza Jarosław Baranowski.
Ważnym elementem wdrożonego rozwiązania jest bezpieczeństwo. Każde ze stanowisk zostało wyposażone we własny, niezależny układ, uruchamiający automatyczne wyłączenie stacji w przypadku stwierdzenia nieprawidłowości. Wystąpienie zdarzenia związanego z naruszeniem bezpieczeństwa na pojedynczym stanowisku nie powoduje jednak unieruchamia całej linii produkcyjnej. Dzięki temu, może ona działać i wykonywać pozostałe prace równolegle, a po usunięciu awarii możliwe jest wznowienie prac na unieruchomionym stanowisku.
ZOBACZ TAKŻE

Gorący tematValeo planuje redukcje zatrudnienia i zamknięcie dwóch fabryk. Ominą czechowickie zakłady

W Ligocie otwarto market Dino. To drugi obiekt tej sieci w naszej gminie
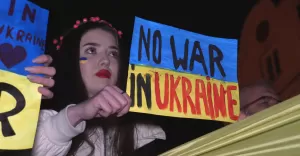
Unia Europejska przedłuża zwolnienia z cła i VAT na pomoc dla ofiar wojny w Ukrainie

W Bielsku-Białej powstanie nowy sklep sieci IKEA. Otwarcie jeszcze w tym roku
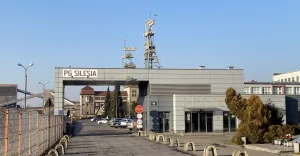
W końcu dobre wiadomości z PG Silesia. Jest umowa sprzedaży węgla za 20 mln zł

Czechowicka firma strategicznym partnerem spółki z polskiego rynku rajdów samochodowych
Komentarze
Zgodnie z Rozporządzeniem Ogólnym o Ochronie Danych Osobowych (RODO) na portalu czecho.pl zaktualizowana została Polityka Prywatności. Zachęcamy do zapoznania się z dokumentem.